Setting Up and Operating an Air Compressor Safely
Air compressors are versatile tools that can be used for a wide range of tasks including drilling, hammering, sanding, grinding, cutting, nailing, stapling, wrenching, and more. They are suitable for both amateur DIY enthusiasts and trade experts. Our inventory includes a wide variety of compressors and air tools to choose from. Once you have selected the right air compressor for your needs, the next step is to learn how to set it up and use it safely.
Ask our team1. Safety:
Remember to wear safety gear, such as goggles and safety boots. Safety boots are particularly important when handling heavy materials or using pneumatic nailers and staplers.
2. Avoid Extension Leads:
When using an air compressor, avoid using a power extension lead. Instead, opt for a hose reel extension. This is because an air compressor may experience voltage dropouts if the mains lead is longer than what is recommended. Utilizing air hose extensions is a better option as it allows flexibility in maneuvering the air tool around the workspace. It’s crucial to select the appropriate air hose for the specific job. You can find more information in our upcoming buying guide for air compressor hoses.
3. Check Oil Level
Keep an eye on the compressor oil level through the sight glass. The oil should be at the same level as the ‘red dot’. If it’s lower and needs topping up, remove the filler plug, and add oil slowly. Also, remember to lubricate your air tools regularly to protect them and extend their working life.
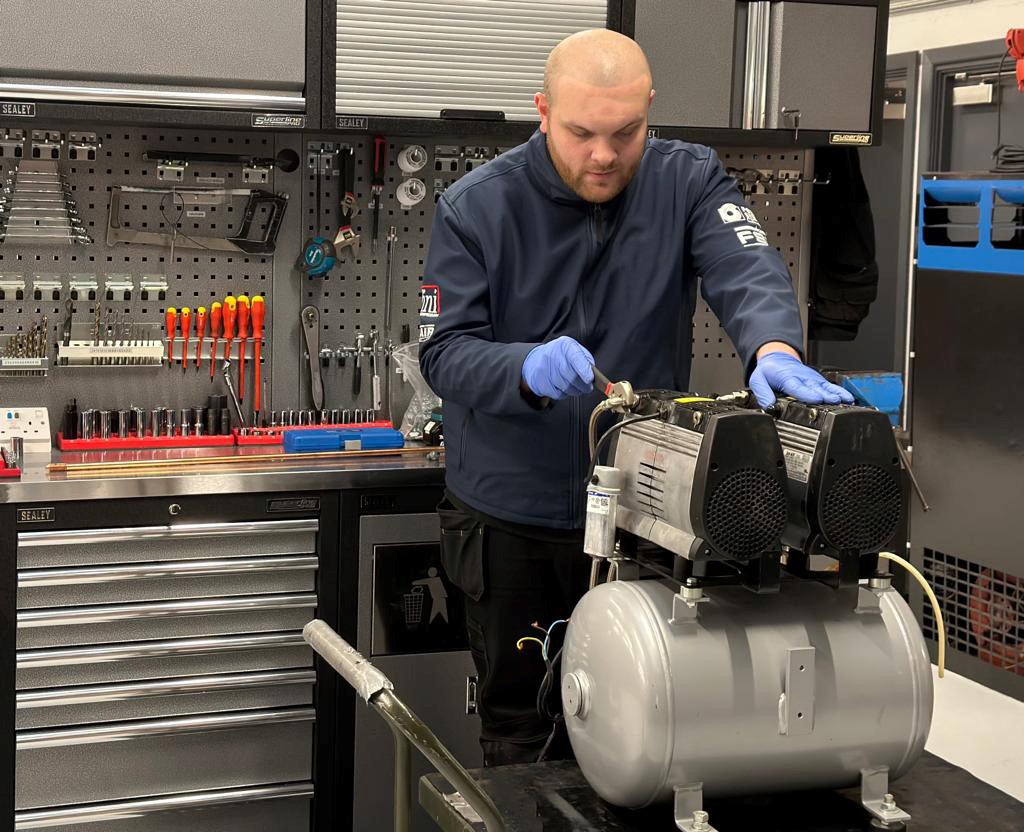
4. Attach an air filter:
An air filter’s role is crucial because it protects compressor components from airborne debris, reducing downtime and repairs in maintaining clean air during tasks such as paint spraying.
5. Insert oil bung
Insert the air bung into the top of the motor. The air bung acts as a vacuum for the oil part of your compressor and allows the system to ‘breathe’ properly.
6. Power On
To power the air compressor, pull the compressor power switch up. If you need to stop the compressor then simply push the switch down.
7. Fill the Tank
Once the compressor is turned on, the tank will automatically fill to its maximum pressure of 8 bar. The compressor will then switch itself off until you start using the air supply with your tool, and automatically switch back on again when the tank needs to be refilled.
8. Connect an Air Hose
Plug in an air hose. Our compressors all use standard Euro-type quick-release fittings. We also offer a wide range of fittings, including PCL, Euro, and QR100.
9. Connect an Air Tool
Attach the desired air tool to the air hose. If an in-line oiler is not in use, then introduce a few drops of oil into the coupler, and reapply oil after approximately 10-15 minutes of tool operation.
10. Set Regulator
Please ensure to adjust the air regulator by turning it clockwise until you attain the precise pressure required. It is important to refer to the relevant manual for each tool to establish the appropriate operating pressure.
11. After Use
After using your air compressor, rotate the air regulator counterclockwise to shut off the valve.
12. Power Off
Turn off the compressor power switch. Disconnect the compressor from the power outlet and let the unit cool down before storage, as the motor can become very hot during use.
13. Drain the Tank
Drain the air and moisture using the ball valve/ drain valve underneath the tank after each use. This stops any moisture getting into your work via any air tools that are connected. If you struggle with conducting this after every use, you can fit an automated drain.
14. Thermal Cut Off
The thermal cut-out reset switch is typically situated close to the oil sight glass for easy access in case the compressor overheats and shuts off.
Would you like to learn more?
We would be thrilled to talk more.
Ask our teamHow to Set Up & Use an Air Compressor Safely
Tips & Tricks
It is imperative to prioritize self-care, the well-being of others, and the maintenance of your air compressor equipment. Similar to all machinery, your compressor necessitates regular maintenance to ensure optimal performance. Kindly refer to our Air Compressor Maintenance Tips provided below.
Read and Follow Your Air Compressor’s Manual
Failing to thoroughly read the product manual can lead to rapid damage to an air compressor. Despite being a low maintenance device, the manual contains straightforward tips that can help extend the lifespan of your air compressor significantly. Moreover, neglecting the guidelines in the manual may risk invalidating the two-year warranty.
Clean/Replace air Intake Filter
A dirty air filter can cause the intake valve to work harder to draw in air. It’s crucial to keep the intake filter of your compressor clean, particularly when operating in a dirty or dusty environment like a garage or workshop. Locate your machine’s air filter and remove it either by pinching it out with your fingers or by unscrewing the screws that hold it in place. Installing a new filter is typically as simple as reversing the removal steps.
Drain off Condensate and Moisture
An air compressor tank will collect moisture from the compressed air, especially when used in a humid environment. Most tanks are equipped with a valve to drain this accumulated moisture, and it is crucial to drain it regularly. Always remember to release the air pressure from the tanks before draining the water.
Check all Hoses and Valves
It’s essential to check all hoses and valves regularly. Cracked or corroded parts can lead to air leaks, putting undue stress on your air compressor’s other components as they work harder to meet the demand. If you discover any cracks or damage, replacement is necessary, as repairs are not feasible. Additionally, the vibration from the running air compressor can loosen screws, nuts, and bolts, so it’s important to inspect and tighten them periodically to ensure everything remains secure.
Check/Change Engine Oil
Begin by removing the fill cap to allow air into the system, then take out the plug from the compressor tank to drain the oil into a container. After all the old oil is drained, reinsert the drain plug with an adjustable wrench. Proceed to fill the machine slowly with high-quality air compressor oil or the oil recommended by your manufacturer, ensuring the correct amount is added. Typically, this maintenance should be performed every 4000 hours of operation, or at least once a year for those who use the compressor less frequently.
For the longevity of your air compressor;
Repairs
Repairs must only be carried out by a qualified engineer, If problems occur, contact us on 01217533330.
Power off
Ensure that the pressure is fully released from the air tank and the compressor is unplugged from any electrical source before beginning any maintenance work.
Release the pressure
Ensure to release any pressure from the storage tank after use, if storing the air compressor overnight or when transporting.
Avoid poor conditons
Avoid operating in wet or damp environments and ensure your compressor remains dry at all times. Clean air is essential for optimal compressor performance. Refrain from using it in dusty or dirty areas without the correct filtration in place.
Would you like to learn more?
We would be thrilled to talk more.
Ask our team