Case Study
Saving Energy in Tight Spaces!
Company Background:
Since 2020, Ultron Technologies has been at the forefront of innovation, offering a comprehensive array of in-house designed modules for seamless smart connectivity. Their product lineup includes advanced Bluetooth solutions (classic and Bluetooth Low Energy), high-speed Wi-Fi, reliable GSM, versatile RF, and cutting-edge IR-enabled devices. These products are engineered to effortlessly connect multiple assets, utilising a combination of wired and wireless protocols for enhanced performance and flexibility.
The Challenges:
Ultron Technologies relies heavily on compressed air to manufacture printed circuit boards (PCBS) and various technical electrical equipment. However, their current system operates at full capacity around the clock, resulting in excessive energy consumption and operational inefficiencies. This relentless demand strains resources and drives up costs, highlighting the need for a more optimised and sustainable solution.
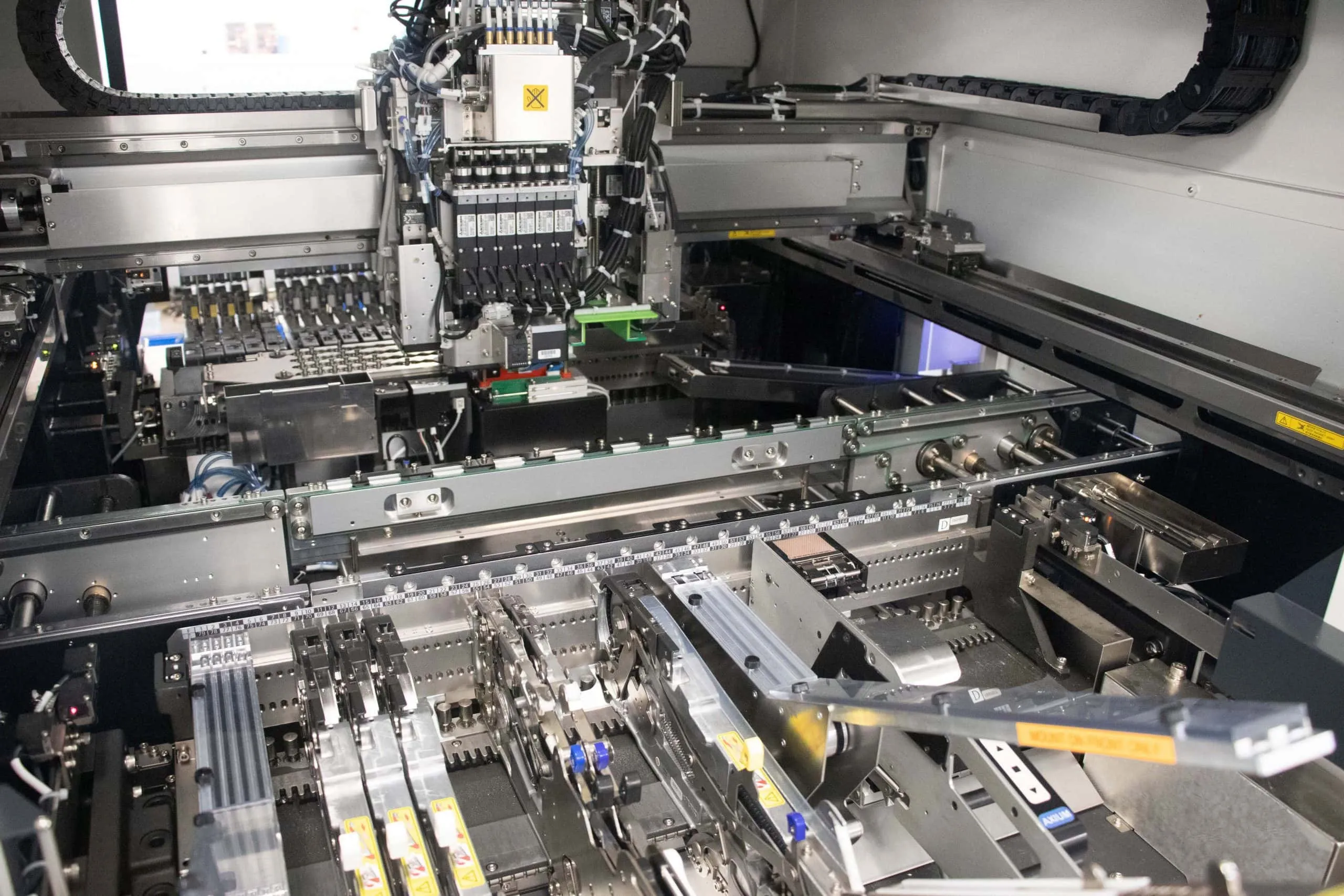
The need for change:
Ultron Technologies recognised the importance of addressing this as part of their dedicated growth strategy, and after completing some energy monitoring, realized their compressed air supply was a significant energy drain.
Ambitious targets and objectives.
Ultron Technologies’ primary objective was to reduce energy consumption in manufacturing while implementing a solution that allows for future expansion of compressed air usage with new equipment when needed. They also considered the constraints of limited space. The company is dedicated to minimising energy consumption in its manufacturing processes. It was seeking an innovative solution that not only lowers energy usage but also accommodates future compressed air applications for new equipment as necessary. Additionally, they needed to address the challenges posed by limited space, ensuring that any proposed solution is efficient and adaptable to their changing requirements.
Focus on the things that matter most.
Ultron Technologies’ main goal was to reduce energy consumption. The solution they adopted allows for variable compressed air. In the past, their compressed air system operated at full capacity continuously, resulting in unreliable air. However, the new system efficiently supplies only the needed power, resulting in significant energy savings.
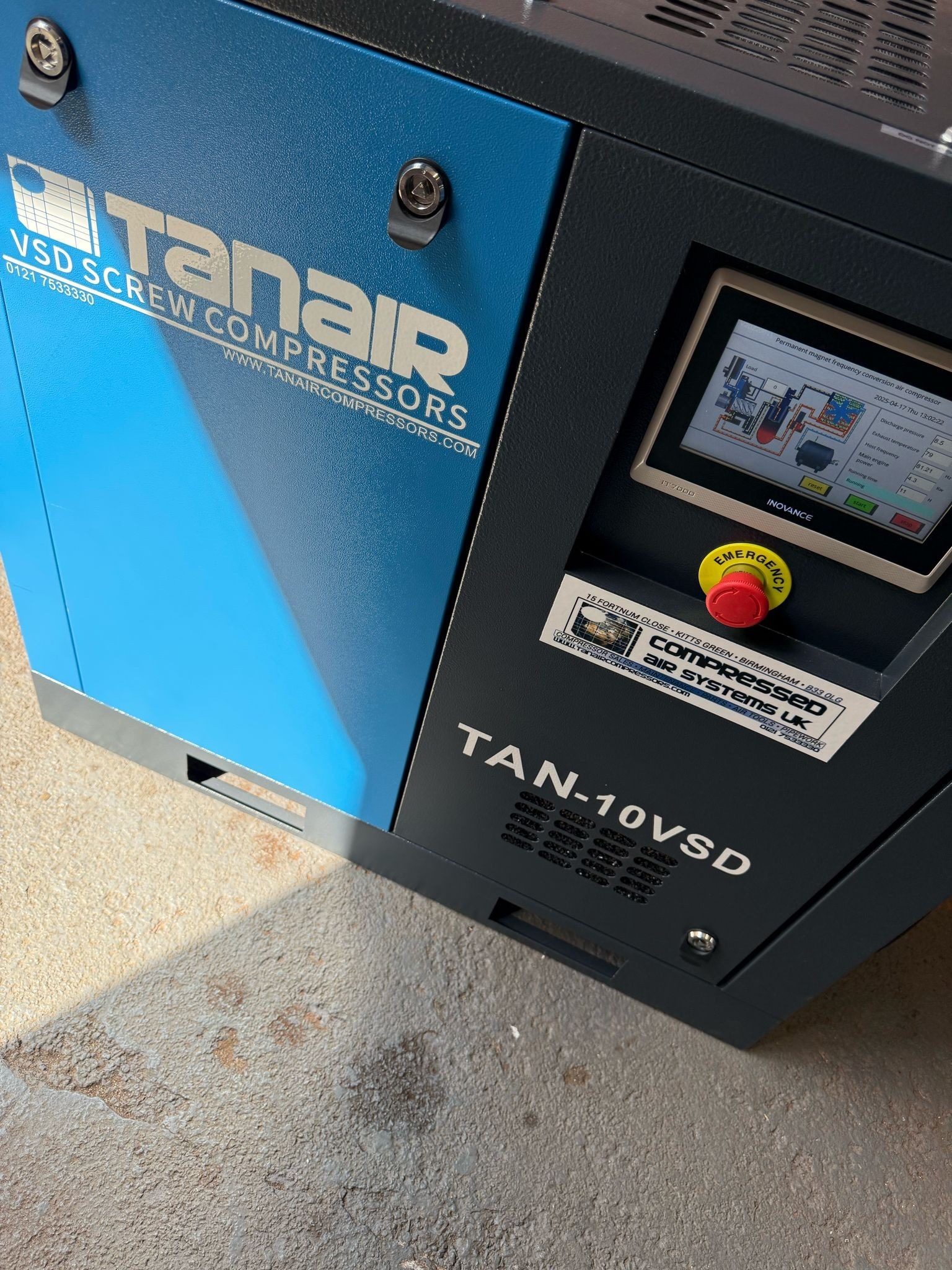
Our Solution:
Their old Champion KA4 was undersized for its intended application. With Ultron’s fast-paced growth, it was not a reliable solution, which is essential for ensuring smooth and efficient operations within the production facility. Due to the various shift patterns, the compressor has faced significant reliability challenges, resulting in inconsistent output that did not meet the increasing demands of production activities.
We proposed an advanced replacement unit to improve flow efficiency while significantly reducing energy consumption. This state-of-the-art unit will feature an inverter-controlled DC permanent magnet motor utilising the latest technological innovations. This sophisticated system allows for precise adjustments in flow rate and pressure output tailored to the specific needs of your application, thereby minimising energy waste typically associated with fixed-speed units.
Additionally, we suggested relocating the Champion compressor to a dedicated outdoor shed enclosure. This well-designed enclosure will be a reliable backup compressor unit storage solution, ensuring uninterrupted operations during maintenance or unexpected downtimes. We incorporated adequate lighting, power, and space within the enclosure to enhance safety and facilitate maintenance. Furthermore, we integrated the existing dryer with the new energy-efficient compressor, connecting it to the backup system.
Our proposal also included using the current compressor vessel as the leading air receiver for the entire setup, optimising space and operational functionality with an EZ1 fitted for ultimate ease of use. The EZ1 will automatically drain the condensate, requiring no manual intervention.
Implementation:
The transition to the new TAN10-VSD/10 Floorpack (415 Volt) | 41 CFM 10 Bar Floor Mounted Variable Speed Air Compressor was seamless, with comprehensive training ensuring proficiency in operation.
The Champion KA4 backup compressor was strategically installed in a well-ventilated and well-lit shed. The 6′ x 8′ enclosure featured double doors and high-level vents, effectively freeing up valuable space in their warehouse, which is increasingly essential given the constraints of operational space.
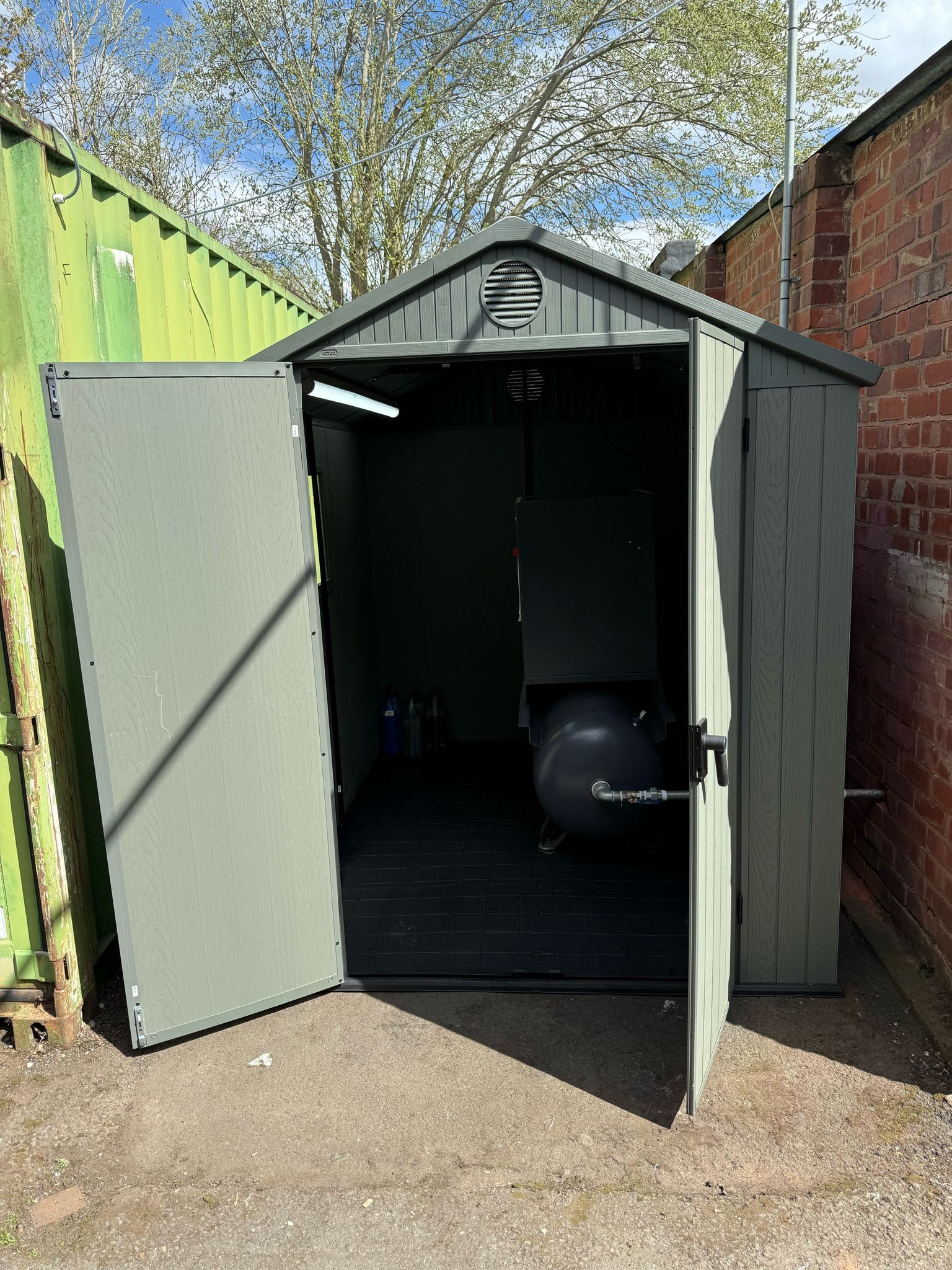
Results:
Following the installation, Ultron Technologies experienced remarkable enhancements in energy efficiency, all while ensuring seamless manufacturing operations. Key highlights of this transformation include a significant reduction in energy consumption across manufacturing processes, allowing for both cost savings and environmental benefits. Additionally, the transition was executed without interruptions, ensuring operations continued smoothly and without downtime. This successful integration showcases Ultron’s commitment to sustainable practices and operational excellence.
Compressed air: an essential force driving efficiency and innovation!
Compressed air plays a pivotal role in their manufacturing operations. By optimizing energy costs, they enhance efficiency and significantly boost their bottom line. It’s a smart business strategy that can’t be overlooked!
Working with good partners.
Ultron Technologie had a fantastic experience with Compressed Air Systems UK. Every member of the team we interacted with demonstrated impressive knowledge and expertise, guiding us toward an ideal solution tailored to our needs. The installation process was seamless and efficient, ensuring minimal disruption to our operations. Additionally, the training provided was thorough and engaging, equipping us with the skills and confidence to make the most of our new system. Overall, it was an outstanding partnership that exceeded our expectations.
The Proof is in the Results
Champion KA4 (Old Compressor) Operating Cost: With a 4 kW compressor load operating at 4 kWh and an electricity rate of £0.30 per kWh, the cost amounts to £1.20 per hour. Over a typical 12-hour day, this totals approximately £13.44, culminating in an annual running cost of £3,494.40 based on 260 working days.
Tanair TAN10-VSD/10 (New Compressor) savings: We anticipate an average energy reduction of over 32.5%, achieved through slower rotation and innovative inverter operation, which delivers precise flow and pressure with minimal unloading waste. The proposed annual running cost is projected to be around £2,358.45, depending on production demands. Impressive!
Would you like to take part in our next case study?
We would be thrilled for you to join us! Contact us