The Importance of Service Contracts and 24/7 Support in Preventing Air Compressor Failures
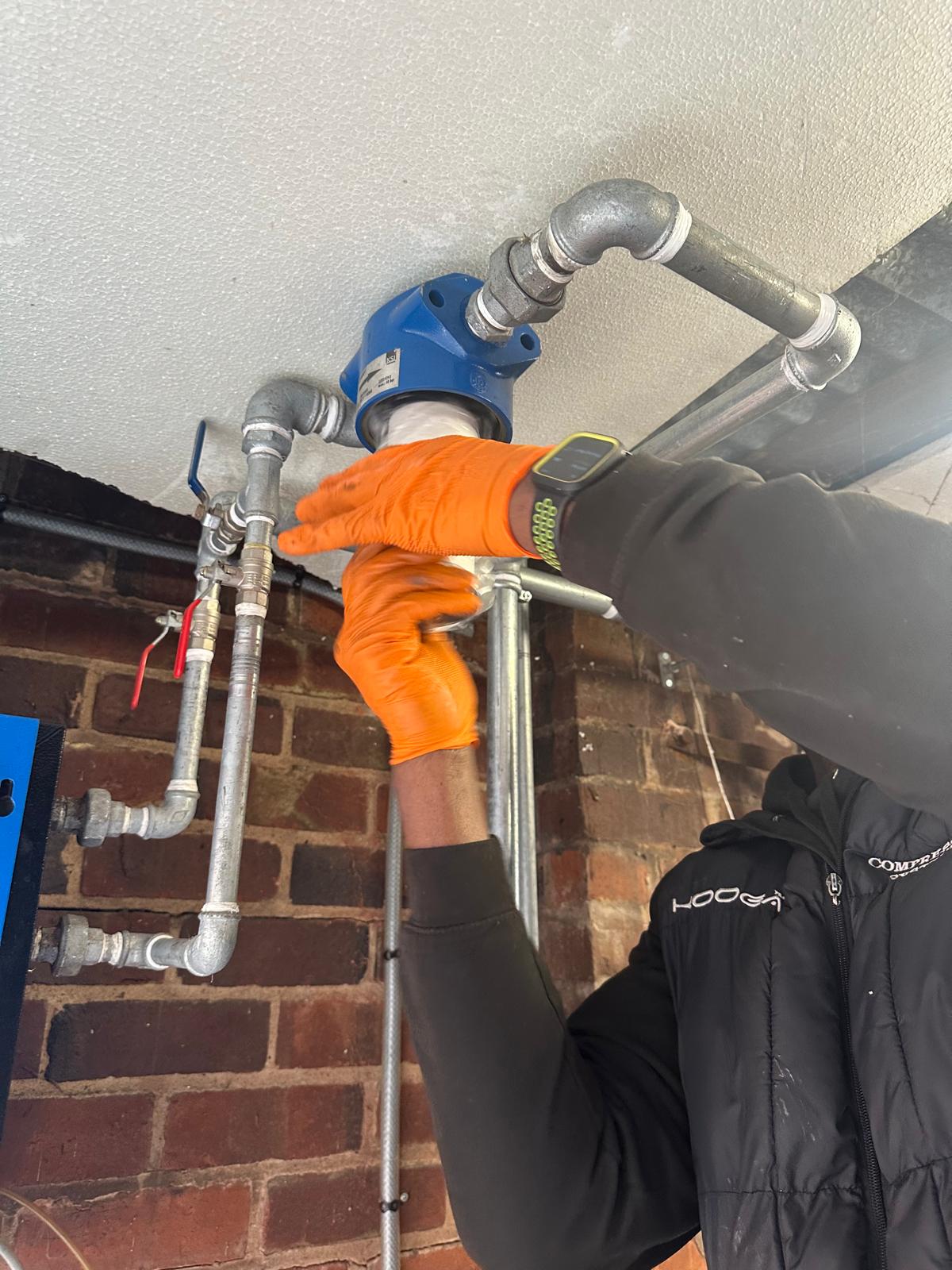
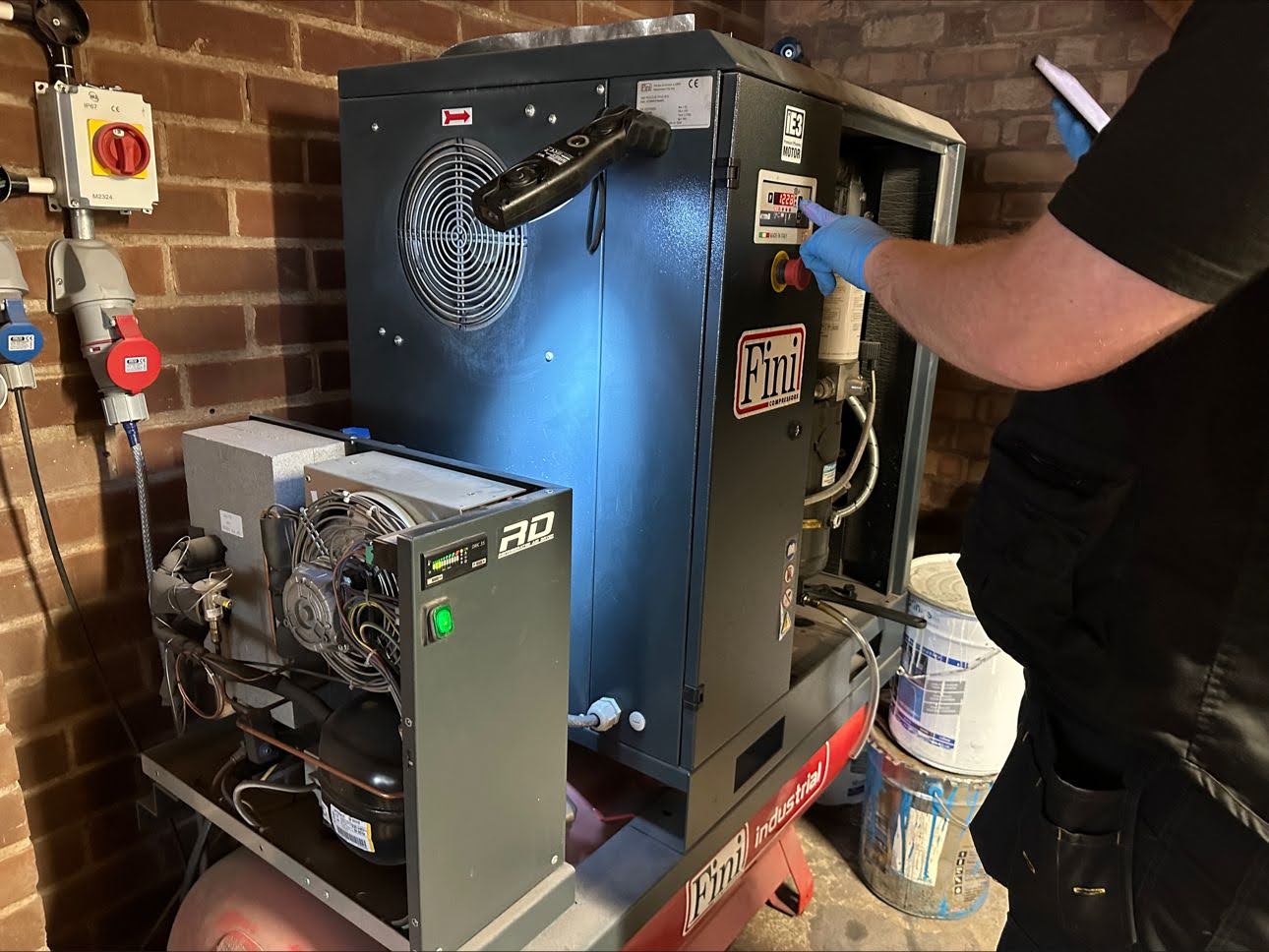
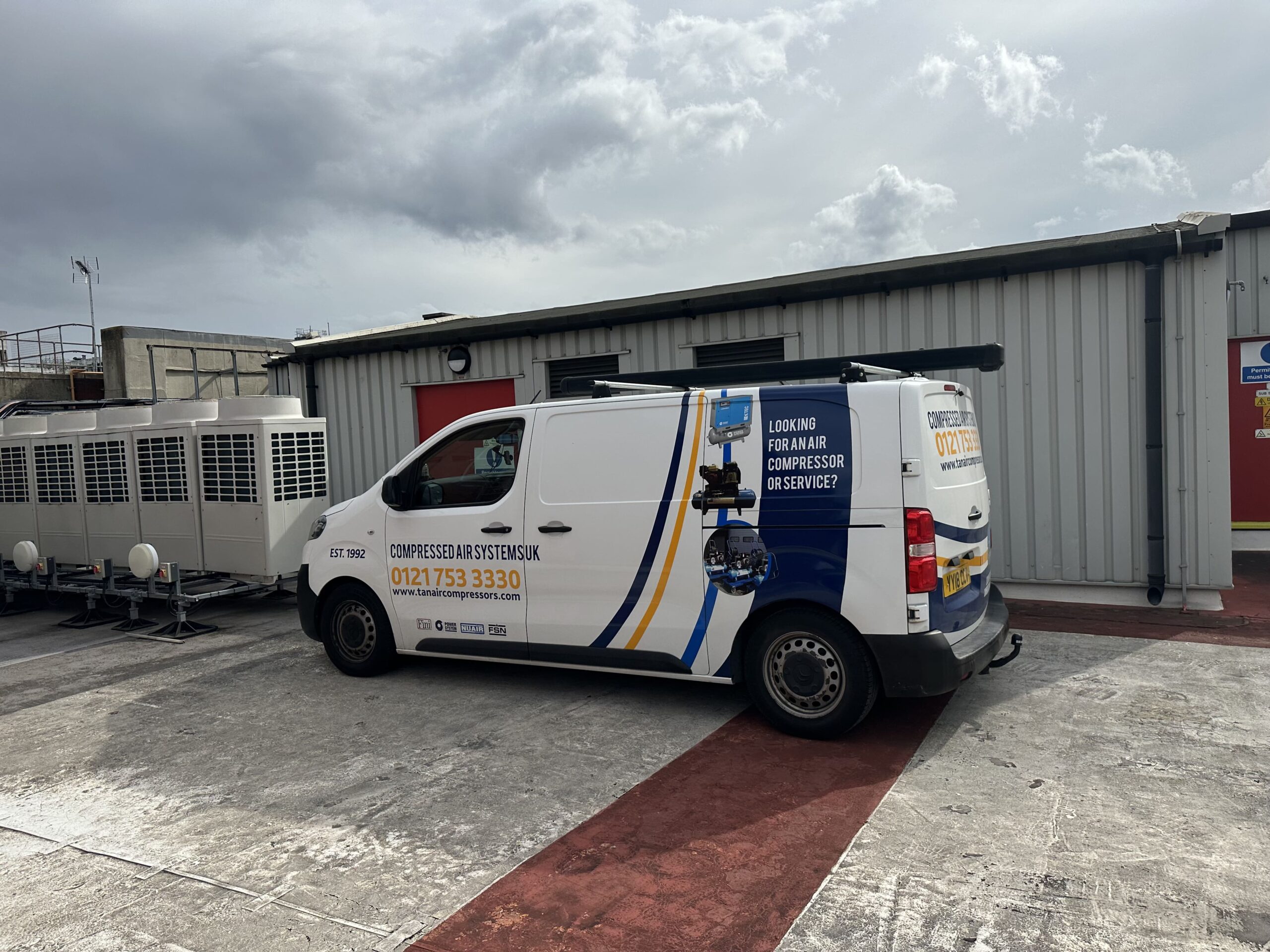

If your business uses an air compressor, it is essential to keep up with maintenance and servicing to ensure that your equipment is properly maintained under the Compressed Air Regulations Act 1996.
Air compressors play a crucial role in a variety of industries, including manufacturing, food production, and automotive assembly. Their reliability and efficiency in providing compressed air make them essential for many operations, from powering pneumatic tools to facilitating complex production tasks.
For example, In the food and beverage industry, clean and contaminant-free compressed air is vital for processes such as bottling, packaging, and cooling products. This helps maintain both quality and safety standards. Similarly, in manufacturing, air compressors are key to powering machinery, enhancing productivity, and reducing human error, which in turn streamlines operations.
Our service contracts are designed to protect your investment and ensure compliance with the Compressed Air Regulations and the Pressure Systems Safety Regulations (PSSR). The Work in Compressed Air Regulations 1996 are a set of regulations in the United Kingdom that govern the health and safety of people working with compressed air.
What do the regulations cover?
Under domestic law (the Health and Safety at Work etc Act 1974) employers are responsible for ensuring the safety of their employees and others. This responsibility is reinforced by regulations.
Many of the duties are placed on compressed air contractors. This reflects the practical operation of the industry and recognises the fact that the contractor in charge of the compressed air operations is best placed to manage and control the health and safety risks of such work. The regulations require the appointment of a Contract Medical Adviser to provide occupational health advice on all aspects of the work in compressed air. A requirement for oxygen breathing during decompression was introduced in 2001.
Because of the number of people required to carry out and manage the work the Construction (Design and Management) Regulations 2007 apply to compressed air projects. For most, but not necessarily all, projects the compressed air contractor will be the principal contractor under these Regulations. Additional requirements relating to emergencies, fire precautions and welfare are set out in the Work in Compressed Air Regulations because of the risks and conditions involved.
Why are these regulations important?
Compressed air can cause serious injuries, even at low pressures, as it can enter the bloodstream through skin breaks or body openings, leading to air bubbles in the blood. Therefore, it is crucial for us to inform you of these obligations.
Compressed Air Systems UK recommends servicing your compressor every 2,000 working hours. This is essential because compressed air applications operate more efficiently when the air is clean, dry, and free from contamination. Neglecting routine maintenance can allow contaminants into the compressor, potentially shortening the lifespan of system components and leading to costly repairs and downtime for your operations.
To ensure the longevity, efficiency, and reliability of your compressed air system and its components, maintenance must be performed according to the Original Equipment Manufacturer (OEM) recommendation of servicing every 2,000 hours. Air compressor components have limited lifespans, as outlined in your service contract. For example, an air filter or oil filter typically lasts for 2,000 hours. While they may occasionally exceed this timeframe, continued contamination increases the likelihood of breakdowns.
The Significance of Operational Efficiency and Reducing Downtime
Operational efficiency is crucial since any downtime caused by air compressor failures can lead to significant financial losses. Industries that rely on compressed air often face major challenges when their systems fail, resulting in halted production lines, delayed deliveries, and increased operational costs. Therefore, maintaining optimal performance through regular servicing and timely support is essential to minimize these risks. Our service contracts are vital for many businesses, providing security for their operations and ensuring minimal downtime.
Our service contracts can benefit your business in multiple ways. If you require further information, please don’t hesitate to reach out.
Benefits of a service contract with Compressed Air Systems UK
-
Reduce Electricity Bills
-
Ensure Equipment is correctly maintained under the Compressed Air Regulations Act 1996
-
Ensure Equipment performs at optimum performance and runs efficiently.
-
Ensure Compliance with Pressure System Safety Regulations (PSSR)
-
Eliminate Premature Breakdowns and Eliminate Loss of Production
-
Extend Equipment Life
-
Ensure High Resale Value
Our dedicated teams are always ready to assist, ensuring minimal disruption and maximum efficiency for your operations.
The Importance of 24/7 Assistance
The importance of 24/7 assistance for air compressor maintenance and support cannot be overstated. Continuous support ensures that any issues are addressed promptly, preventing prolonged downtime and safeguarding productivity. With effective support, businesses can protect their operations and enhance overall efficiency, allowing them to concentrate on growth and innovation.
At Compressed Air Systems UK, we recognize the critical need for reliable air compressor systems. We are dedicated to providing comprehensive support to ensure our customers can operate at their best, around the clock. We proudly offer our services to a wide range of areas, including:
- Chesterfield,
- Corby,
- Coventry,
- Daventry,
- Derby,
- Derbyshire,
- Dudley,
- East Lindsey,
- Erewash,
- Gedling,
- Harborough
- Herefordshire,
- High Peak,
- Hinckley and Bosworth,
- Kettering,
- Leicestershire,
- Lichfield,
- Lincoln,
- Lincolnshire,
- Malvern Hills,
- Mansfield,
- Melton,
- Rutland,
- Sandwell,
- Shropshire,
- Shropshire,
- Solihull,
- South Holland,
- South Kesteven,
- Staffordshire,
- Staffordshire,
- Stoke-on-Trent,
- Stratford-on-Avon,
Our Service Contract Packages
Our service contract packages offer numerous benefits, and we provide several options for you to choose from. Please keep reading to find out more.
Our Standard Package
Our standard package is tailored for individuals looking to predict future expenses associated with their service visits. It is affordable and includes preventative measures, along with flexible payment options. This package is ideal for those who operate around 4,000 hours per year or less, which is approximately equivalent to working five eight-hour days each week.
Each service visit includes:
Change of serviceable components to include Air Filter, Oil Filter and Separator (as per OEM schedule) | ✔ |
Discounted Genuine Spare Parts and Lubricants | ✔ |
Discounted Labour & Travel Charges @ an agreed rate | ✔ |
Options of 2, 3, 4 or 5-year contracts | ✔ |
Environmental disposal of used Lubricant | ✔ |
A Check of the compressor operations | ✔ |
A check of the drive couplings/ bearings (where applicable) | ✔ |
A check of the auto drains (where applicable) | ✔ |
A check of the electrical terminals | ✔ |
A check for any oil or air leaks | ✔ |
Cleaning of the machine and associated equipment. | ✔ |
Pay-per-visit or Interest-Free Monthly Payments | ✔ |
Our Intermediate Package
Our intermediate package is designed for companies who want to forecast future expenses related to their service visits, including preventative parts as recommended by the original equipment manufacturer (OEM). It is cost-effective and incorporates preventative measures, along with flexible payment options. This package is ideal for those who operate for more than 4,000 hours per year, which is roughly equivalent to working more than five eight-hour days each week.
Each service visit includes:
Change of serviceable components to include Air Filter, Oil Filter and Separator (as per OEM schedule) | ✔ |
Change of remedial parts as per OEM recommendations | ✔ |
Discounted Genuine Spare Parts and Lubricants | ✔ |
Discounted Labour & Travel Charges @ an agreed rate | ✔ |
Options of 2, 3, 4 or 5-year contracts | ✔ |
Environmental disposal of used Lubricant | ✔ |
A Check of the compressor operations | ✔ |
A check of the drive couplings/ bearings (where applicable) | ✔ |
A check of the auto drains (where applicable) | ✔ |
A check of the electrical terminals | ✔ |
A check for any oil or air leaks | ✔ |
Cleaning of the machine and associated equipment. | ✔ |
Pay-per-visit or Interest-Free Monthly Payments | ✔ |
Our Comprehensive Package
Our comprehensive package is tailored for companies looking to forecast future expenses related to service visits. This includes costs for preventative parts recommended by the original equipment manufacturer (OEM) and all unavoidable breakdowns. It is cost-effective and includes preventative measures along with flexible payment options. This package is optimal for companies that operate more than 8,000 hours per year, which is equivalent to working 24/7.
Each service visit includes:
Change of serviceable components to include Air Filter, Oil Filter and Separator (as per OEM schedule) | ✔ |
Change of remedial parts as per OEM recommendations | ✔ |
Discounted Genuine Spare Parts and Lubricants | ✔ |
Discounted Labour & Travel Charges @ an agreed rate | ✔ |
Options of 2, 3, 4 or 5-year contracts | ✔ |
All callouts within the course of the contract | ✔ |
Environmental disposal of used Lubricant | ✔ |
A Check of the compressor operations | ✔ |
A check of the drive couplings/ bearings (where applicable) | ✔ |
A check of the auto drains (where applicable) | ✔ |
A check of the electrical terminals | ✔ |
A check for any oil or air leaks | ✔ |
Cleaning of the machine and associated equipment. | ✔ |
Pay-per-visit or Interest-Free Monthly Payments | ✔ |
We are excited to highlight that we maintain an extensive inventory of spare and service parts for a wide range of compressor manufacturers, ensuring your needs are met promptly and efficiently.
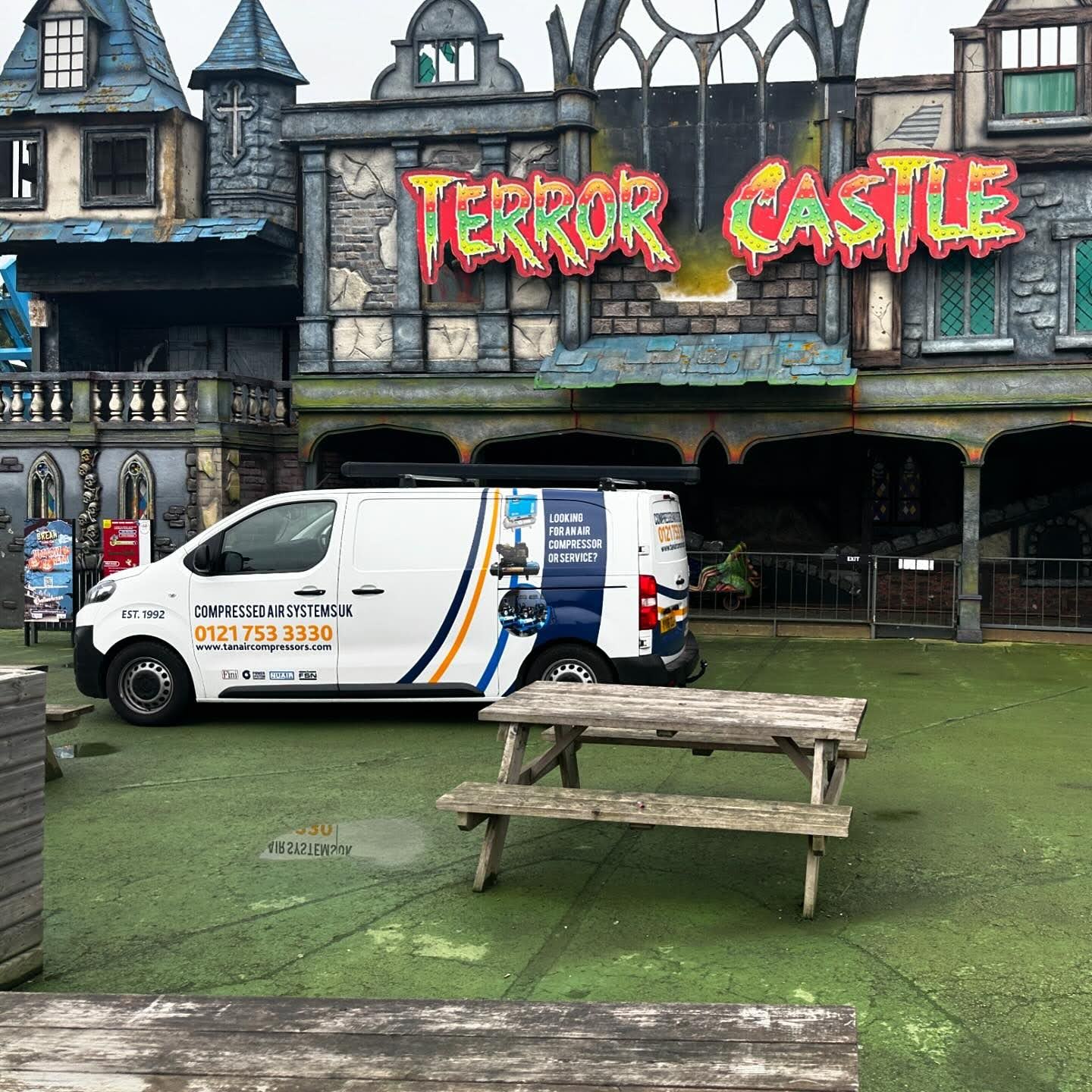
Advantages of service contracts and our 24/7 Support
The benefits of our 24/7 assistance are evident:
Reduced Downtime and Associated Costs: Quick response times minimize downtime, helping businesses maintain productivity and reduce financial losses.
Enhanced Operational Efficiency: Continuous support enables businesses to operate smoothly, ensuring that their air compressors function optimally at all times.
Improved Safety and Compliance with Regulations: Regular maintenance and immediate support ensure compliance with safety regulations, protecting both employees and the business.
At Compressed Air Systems UK, we recognize the critical need for reliable air compressor systems and the importance of 24/7 assistance in keeping your operations running smoothly.
Strategies for Establishing a 24/7 Support System
Implementing a robust 24/7 support system for air compressors is essential for ensuring uninterrupted operations. Here are some key strategies for establishing such a system:
In-House vs. Outsourced Support
Businesses must decide whether to maintain an in-house support team or outsource to a specialized service provider.
In-House Support: This option allows for greater control and quicker response times since technicians are readily available on-site. However, it requires significant investment in training and resources. If this is something you are interested in, our team are here to help with facilitating this.
Outsourced Support: Partnering with an external service provider can offer access to a wider range of expertise and resources without the overhead costs of maintaining a full-time team. This can be particularly beneficial for all businesses, regardless of size.
Conclusion
In conclusion, implementing a 24/7 support system for air compressors is not just a luxury but a necessity for businesses that rely on these systems for their operations. By establishing effective strategies, leveraging technology, and ensuring proper training and resources, companies can significantly reduce downtime, enhance operational efficiency, and ultimately save costs.
At Compressed Air Systems UK, we are committed to providing our customers with the support they need to keep their air compressor systems running smoothly, day and night. Our expertise and comprehensive service offerings ensure that your operations can thrive without interruption.
24/7 Support for Your Air Compressors
At Compressed Air Systems UK, we understand that the reliability of your air compressor systems is critical to your operations. That’s why we offer comprehensive 24/7 support tailored to meet your needs. Whether you require immediate assistance, routine maintenance, or expert advice, our dedicated team is here to help you every step of the way.
Why Choose Us?
Factory Trained Engineers: Our engineers have been factory-trained in all aspects of compressed air. Certificates are available upon request.
Immediate Response: Our skilled technicians are available around the clock to address any issues and minimize downtime.
Expertise You Can Trust: With over 30 years of experience in the industry, we provide unparalleled support and knowledge.
Advanced Technology: We utilize the latest monitoring and diagnostic tools to ensure your systems are operating at peak performance.
Get in Touch Today!
- Phone: Call us at 01217533330
- Message: Send us a message through our website or email.
- Chat: Connect with us through our live chat feature on our website.
We pride ourselves on our responsiveness and 24/7 monitoring to ensure your peace of mind. You can also visit our offices, trade counter, and warehouse at:
Compressed Air Systems UK
Unit 15, Fortnum Close, Birmingham, B33 0LG
Read our Latest Reviews
We had a Clarke for a couple of years that we abused running it 12 hours a day. We found CAS UK when it needed a repair, and we were very impressed with how quickly they responded and came out to repair and service the machine.
Our business started to expand and we needed a large compressor with a proper airlines feeding our machines and work stations. The guys from CAS supplied the new compressor and worked flat out getting the machine and pipe working in.
They're a brilliant group of lads with a great work ethic and really easy to communicate with.
We'll 100% continue to use and recommend them.
Very efficient at every level.
Quite a rare find ~ don't waste the opportunity if you have a need within their expertise. Mike Fisher
Compressor delivered to my premises in what was a great service by Compressed Air Systems UK. Thanks for a great experience
Never let me down!
Always been brilliant & came out the same day if there is ever an issue.
Thank you
Jordan
Very professional always great advisor for the best machine for what we need, friendly office staff and most of all the knowledge from them is second to none.
Would recommend to anyone that needs advise or want to buy the right machine for them.
Plus the backup you get is the best.
I was advised well and even advised towards a better value option saving us a chunk of money. Top quality honest service all round...... Thanks again.